Introduction
Diesel generators play a crucial role in providing backup power in various industrial settings. Their reliability and efficiency are vital to ensuring uninterrupted operations during power outages. To guarantee the performance of diesel generators before deployment, factory acceptance testing (FAT) is conducted. This article will delve into the importance of diesel generators in industrial applications, the significance of FAT in ensuring their reliability, the key components of FAT for diesel generators, and best practices for conducting successful FAT processes.
Importance of Diesel Generators in Industrial Applications
Diesel generators are widely used in industrial settings to provide backup power during outages or as a primary power source in remote locations. These generators are preferred for their reliability, durability, and ability to provide continuous power for extended periods. In industries such as manufacturing, oil and gas, telecommunications, healthcare, and data centers, a reliable power source is essential to prevent disruptions and ensure the safety of personnel and critical equipment.
In industrial applications, diesel generators are commonly used for the following purposes:
1. Backup Power: Diesel generators serve as a reliable backup power source to ensure uninterrupted operations during utility power outages. They can automatically start and take over the load within seconds of a power failure, preventing costly downtime and production losses.
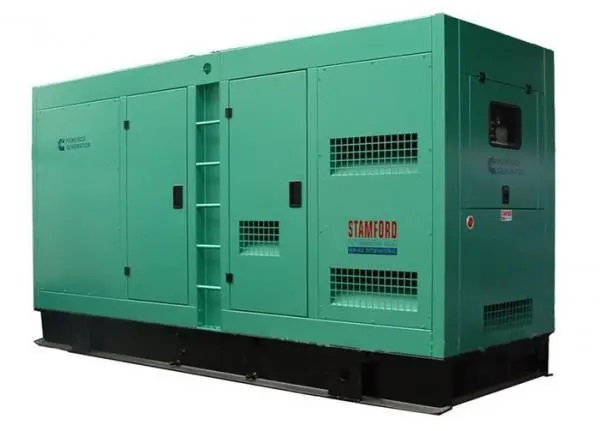
2. Peak Shaving: Diesel generators can be used to supplement grid power during peak demand periods, helping to reduce electricity costs by offsetting high demand charges.
3. Remote Power Generation: In remote locations where grid power is unavailable or unreliable, diesel generators provide a dependable source of power for industrial operations, construction sites, mining facilities, and off-grid installations.
4. Emergency Response: Diesel generators are essential for emergency response and disaster recovery efforts, providing critical power for hospitals, emergency services, communication networks, and essential infrastructure during natural disasters or emergencies.
Overall, diesel generators play a vital role in ensuring the continuity of industrial operations, protecting critical equipment, and safeguarding the well-being of personnel in various industrial sectors.
Significance of Factory Acceptance Testing (FAT) for Diesel Generators
Factory Acceptance Testing (FAT) is a crucial step in the quality assurance process for diesel generators before they are installed and commissioned in industrial settings. FAT is conducted at the manufacturer's facility to verify that the generator meets the specified requirements, standards, and performance criteria outlined by the customer. The primary objectives of FAT for diesel generators include:
1. Verification of Specifications: FAT ensures that the diesel generator complies with the technical specifications, design criteria, and performance parameters specified in the purchase order or contract. This includes verifying the capacity, efficiency, fuel consumption, voltage regulation, and other critical characteristics of the generator.
2. Functional Testing: FAT involves testing the operational functionality of the diesel generator under various load conditions, starting and stopping sequences, synchronization with the grid, and automatic transfer switch (ATS) operation. Functional testing helps identify any issues or deficiencies in the generator's performance before it is delivered to the customer's site.
3. Quality Assurance: FAT is an essential quality control measure to ensure that the diesel generator is manufactured, assembled, and tested according to industry standards, codes, and best practices. Quality assurance during FAT helps prevent defects, malfunctions, or safety hazards that could compromise the reliability and performance of the generator in the field.
4. Documentation and Compliance: FAT includes the review and verification of technical documentation, test reports, inspection records, and compliance certificates related to the diesel generator. Proper documentation during FAT ensures traceability, transparency, and accountability throughout the manufacturing and testing process.
Overall, FAT for diesel generators is a critical step in ensuring the reliability, safety, and performance of the generator before it is installed and commissioned in industrial applications. By conducting thorough FAT processes, manufacturers and customers can mitigate risks, address potential issues, and guarantee the successful operation of diesel generators in the field.
Key Components of Factory Acceptance Testing (FAT) for Diesel Generators
Factory Acceptance Testing (FAT) for diesel generators consists of several key components that are essential for verifying the performance, functionality, and compliance of the generator. The following are the key components of FAT for diesel generators:
1. Electrical Testing: Electrical testing is a fundamental component of FAT for diesel generators, involving the verification of voltage output, frequency regulation, voltage waveform distortion, and transient response under load conditions. Electrical testing ensures that the generator meets the specified electrical parameters and can deliver stable and reliable power to the load.
2. Mechanical Testing: Mechanical testing assesses the mechanical components and systems of the diesel generator, including the engine, alternator, cooling system, fuel system, exhaust system, and control panel. Mechanical testing involves running the generator at various load levels, checking for abnormal vibrations, monitoring temperatures, and assessing the overall mechanical integrity of the generator.
3. Load Bank Testing: Load bank testing is conducted to simulate real-world load conditions on the diesel generator and verify its performance under different load levels, power factors, and transient events. Load bank testing helps identify any issues related to voltage regulation, frequency stability, overheating, or overload capacity of the generator.
4. Control System Testing: Control system testing evaluates the operation and functionality of the generator's control panel, engine governor, automatic voltage regulator (AVR), synchronizing system, and protection relays. Control system testing ensures that the generator can start, synchronize, and operate seamlessly in parallel with the grid or other generators.
5. Performance Testing: Performance testing assesses the overall performance characteristics of the diesel generator, including fuel efficiency, power output, response time, voltage stability, and transient recovery. 75kw diesel generator for temporary housing helps verify that the generator meets the specified performance criteria and can reliably provide power during normal and emergency conditions.
6. Safety and Protection Testing: Safety and protection testing focus on verifying the proper operation of safety features, alarms, shutdown systems, and protection relays installed in the diesel generator. Safety testing ensures that the generator can respond to abnormal conditions, faults, or emergencies to protect personnel, equipment, and the power system.
7. Environmental Testing: Environmental testing evaluates the generator's performance under various environmental conditions, such as temperature extremes, humidity levels, dust exposure, and vibration resistance. Environmental testing helps assess the generator's reliability and durability in challenging operating environments.
By addressing these key components of FAT for diesel generators, manufacturers and customers can ensure that the generator meets the required specifications, standards, and performance criteria before it is delivered and commissioned in industrial applications.
Best Practices for Conducting Successful Factory Acceptance Testing (FAT) Processes
To ensure the effectiveness and efficiency of Factory Acceptance Testing (FAT) for diesel generators, it is essential to follow best practices and guidelines throughout the testing process. The following are some best practices for conducting successful FAT processes for diesel generators:
1. Define Clear Acceptance Criteria: Before conducting FAT, it is crucial to define clear acceptance criteria, performance standards, and testing procedures based on the specifications, requirements, and expectations outlined in the contract or purchase order. Clear acceptance criteria help establish measurable objectives and ensure that the generator meets the desired performance levels.
2. Plan and Prepare in Advance: Proper planning and preparation are essential for conducting successful FAT processes. This includes scheduling the testing activities, coordinating with stakeholders, preparing test scripts and procedures, arranging for necessary equipment and tools, and ensuring that the testing facility is ready for the FAT.
3. Involve Stakeholders: FAT should involve key stakeholders, including representatives from the manufacturer, customer, engineering team, quality assurance team, and end-users. Involving stakeholders in the FAT process promotes transparency, collaboration, and alignment of expectations regarding the generator's performance and compliance.
4. Conduct Comprehensive Testing: Ensure that all critical components and systems of the diesel generator are thoroughly tested during FAT, including electrical, mechanical, control, performance, safety, and environmental aspects. Comprehensive testing helps identify potential issues, validate the generator's performance, and ensure compliance with standards and specifications.
5. Document Test Results: Documenting test results, observations, deviations, and corrective actions during FAT is essential for traceability, accountability, and continuous improvement. Detailed documentation helps track the testing progress, record findings, communicate results to stakeholders, and facilitate the resolution of issues identified during testing.
6. Address Non-Conformities: If any non-conformities, deviations, or deficiencies are identified during FAT, they should be promptly addressed, investigated, and resolved in accordance with established procedures. Addressing non-conformities ensures that the generator meets the required standards, specifications, and performance criteria before delivery to the customer.
7. Conduct Final Acceptance Review: Upon completion of FAT, conduct a final acceptance review to verify that the diesel generator meets all acceptance criteria, performance standards, and contractual requirements. The final acceptance review involves reviewing test reports, documentation, test results, and stakeholder feedback to ensure that the generator is ready for shipment and installation.
8. Provide Training and Support: Before delivering the diesel generator to the customer's site, provide training and support to the end-users, operators, and maintenance personnel on the operation, maintenance, troubleshooting, and safety procedures of the generator. Training and support help ensure the proper and safe operation of the generator in industrial applications.
By following these best practices for conducting Factory Acceptance Testing (FAT) processes for diesel generators, manufacturers, customers, and stakeholders can ensure the successful verification of the generator's performance, reliability, and compliance with standards before deployment in industrial settings.
Conclusion
Diesel generators are essential for providing backup power, ensuring continuity of operations, and safeguarding critical equipment in various industrial applications. Factory Acceptance Testing (FAT) plays a vital role in verifying the performance, functionality, and compliance of diesel generators before they are installed in industrial settings. By conducting comprehensive FAT processes that address key components such as electrical testing, mechanical testing, control system testing, and performance testing, manufacturers and customers can ensure the reliability, safety, and efficiency of diesel generators.
Through proper planning, preparation, stakeholder involvement, documentation, and adherence to best practices, successful FAT processes can be conducted to validate the performance and compliance of diesel generators. By following the guidelines outlined in this article, stakeholders in the industrial sector can enhance the quality assurance process, mitigate risks, and ensure the successful deployment of diesel generators for critical power applications.
In conclusion, the reliability and efficiency of diesel generators for factory acceptance testing are paramount to ensuring uninterrupted power supply and operational continuity in industrial settings. By emphasizing the importance of FAT, addressing key components of testing, and following best practices, stakeholders can uphold the highest standards of quality, reliability, and performance in diesel generator applications.